Edge-Cloud-Computing:
Eine flexible Edge-Cloud richtig aufbauen
Der Druck, die ständig steigenden Datenmengen dort zu verarbeiten, wo sie auch entstehen, wird in der Produktion und Fertigungsindustrie ständig stärker. Flexible Edge-Cloud-Lösungen aus lokalem Edge-Computing – seit Neuestem in Cloudtechnologie programmiert –, künstlicher Intelligenz, Datenvirtualisierung, vermaschten Netzwerkknoten und last, but not least dem 5G-Kommuni- kationsstandard halten ihren Einzug in die industriellen Werkstätten auch in Deutschland. Es zeichnet sich der IT-Trend ab, nur noch die Ergebnisse dieser Vor-Ort-Verarbeitung in die zentralen Instanzen einer Private- oder Public-Cloud zu geben.
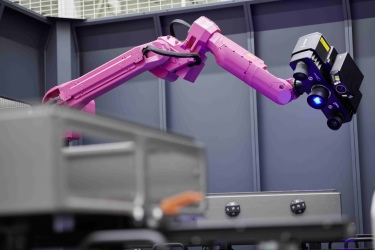
|
|
Vorort-Datenspeicherung in der Produktion.
Bei gängigen betriebswirtschaftlichen Auswertungen kann es einem produzierenden Unternehmen noch relativ gleich sein, ob die Datenverarbeitung, -übertragung und speicherung über die Cloud oder über lokale Server erfolgt. „In beiden Fällen ist die Latenz dafür ausreichend“, sagt Jörg Wende, ausgewiesener Industrieexperte bei IBM Deutschland und als Vertreter von IBM Mitglied in verschiedenen Industrie 4.0-Gremien wie der Plattform Industrie 4.0 und beteiligt bei der Definition der Verwaltungsschale. In der Werkshalle sieht die Sachlage aber schon ganz anders aus. Beim Steuerungszyklus an einer Fertigungsstraße beispielsweise bewegen sich die Taktzeiten typischerweise im Millisekundenbereich. Wende: „Bei allen kritischen Anwendungsfällen, wie z. B. bei der Steuerung von Transportwagen in der innerbetrieblichen Logistik, bei der Kanban-Steuerung und in vielen weiteren Situationen darf am Rand des Netzwerkes nicht unnötig Latenzzeit vergeudet werden, sodass die Vor-Ort-Speicherung und Verarbeitung der Daten oftmals die einzig gangbare Lösung darstellt.“ Darüber hinaus gilt es auch, die Entscheidungslogik IT-seitig nahe dort unterzubringen, wo die Daten anfallen. Ob das komplexe KI-Modelle oder ganz einfach Entscheidungsmatrizen sind, spielt im ersten Schritt noch keine Rolle.
KI in der Produktion – ein Thema über Unternehmensgrenzen hinweg
Künstliche Intelligenz kommt vor allem dort zum Tragen, wo die Verarbeitung von hochvolumigen Videostreamdaten und ähnlichen Datenstrukturen eine Rolle spielt, bei denen im Edge-Bereich mit trainierten Modellen gearbeitet wird. Beim Einsatz in der Produktion gilt es dem IBM-Experten zufolge vor allem, Informationen aus gleichartigen Systemen zentral zusammenzufassen, daraus Lernmodelle abzubilden und diese wiederum an alle Fertigungstraßen zu verteilen. Wende: „Das ist ein Thema nicht nur für einen einzelnen Produktionsstandort, sondern über Werke und Unternehmensgrenzen hinweg.“ An diesen Schritt schließen sich unmittelbar Themen wie u.a. GAIA X an. Es gilt, den Herstellern und ggf. Nutzern über eine sichere europäische Cloudinfrastruktur Verhaltens- und Auslastungsdaten von Getrieben oder Motorpumpen zur Verfügung zu stellen. Damit werden neue Möglichkeiten eröffnet, von einer eher traditionell geplanten Wartung zu vorausschauenden Maintanance-Modellen überzugehen.
„Wir sehen seit vielen Jahren, dass das Datenvolumen an erzeugten Daten wesentlich stärker zunimmt als die Datenbandbreite, die benötigt wird, um die Bits und Bytes an externe Server in der Cloud zu senden“, betont Wende. Gegenüber anderen Branchen oder Industrien ergeben sich für die Produktion und Fertigungsindustrie daraus zwei Besonderheiten: Zum einen wird in der Fertigungshalle selbst zunehmend mit Cloud-Technologie gearbeitet. Technologien aus dem Cloud- und Cloud-Native-Umfeld halten auch in den Fertigungsstätten, am Band, ihren Einzug. Das eröffnet u.a. die Möglichkeit, auch mit containerbasierten Anwendungen zu arbeiten und deren Vorteile wie beispielsweise Skalierbarkeit zu nutzen. Auf der anderen Seite werden aber auch gängige Nachteile fortgeschrieben wie die starke Realtimelastigkeit in einem eher hochfrequenten Umfeld. Wende: „Es liegen noch zu viele Softwareschichten dazwischen, die z. B. bei einer Steuerungssoftware erst noch manuell angepasst werden müssen.“
Die technologische Gretchenfrage beim Edge-Cloud-Computing lautet aber: Wie können Anwendungen zwischen verschiedenen Werksteilen oder Unternehmensteilen problemlos miteinander arbeiten? Im cloudbasierten Umfeld ist das reibungslos möglich, im industriellen Edge-Computing-Umfeld aber heute noch schwierig, weil direkte physikalische Anbindungen an Assets vorliegen, die eine lokale Steuerung übernehmen müssen. Wende präzisiert: „Mit einer Hochofensteuerung kann eben nicht schnell mal eine Walzstraße neu gestartet werden. Ein Neustart muss stets in der gleichen Produktionsumgebung geschehen.“ Edge-Cloud-Lösungen können aber dafür sorgen, dass Verwaltungsschalen immer wieder automatisch aktualisiert werden und synchron bleiben.
Handfeste Vorteile einer flexiblen Edge-Cloud-Infrastruktur
„Gerade in der Produktion und Fertigungsindustrie, wo traditionell sehr viel betagtes Equipment zum Einsatz kommt, das 20 bis 30 Jahre gut funktionieren muss, kann es ein Anreiz sein, die Produktivität über den Aufbau einer flexiblen Edge-Cloud-Infrastruktur zu erhöhen – nicht zuletzt mit dem Vorteil, sehr schnell bessere Entscheidungen treffen zu können“, betont Alexander Körner, IBM-Experte für Edge-Computing und Edge-Analyse im IBM Cloud Engagement Hub. Sowohl Mittelständler als auch Großunternehmen können mit einer flexiblen Edge-Cloud-Lösung ihren Produktionsprozess sukzessive erneuern.
„Auch die Datensouveränität, also sein digitales Tafelsilber nicht so ohne Weiteres außer Haus geben zu müssen, stellt für manchen Industrieanwender einen wichtigen Grund dar, sich mit diesen Themen zu beschäftigen“, weiß Körner zu berichten. Insbesondere für den Schutz sensibler Firmendaten kommt dem kombinierten Einsatz der verschiedenen neuen Edge-Cloud-Technologien vor Ort eine wichtige Bedeutung zu.
Im Hause IBM heiß diskutiert wird auch den im Maschinenbau und in der Produktion bestens bekannten „Digitalen Zwilling“ über die gesamte Wertschöpfungskette – von der Entwicklung und dem Design über die Produktion und Nutzung des Produktes bis hin zum Recycling – mithilfe der neu gegebenen technischen Möglichkeiten abzubilden und in das für den Produktlebenszyklus zuständige System einzubinden.
Big Blue selbst verfügt über das Produkt IBM Edge Application Manager, das dazu verwendet werden kann, einen Edge-Computing Management-Server aufzusetzen um die entsprechenden Zielplattformen – entweder Edge-Clouds oder kleinere Edge-Devices – mehrmandantenfähig darüber zu verwalten. Wende präzisiert: „Auf einen bestehenden Red Hat Open Shift-Cluster setzen wir damit innerhalb einer halben Stunde eine Edge-Cloud auf. Für das Edge-Device liegt der Installationsaufwand bei lediglich fünf Minuten.“
Das Werk Haiger mit 250 vernetzten Maschinen.
Die viel beachtete 5G-Mobilkommunikationstechnologie dagegen gilt bei IBM beim Aufbau einer flexiblen Edge-Cloud-Infrastruktur als reines Mittel zum Zweck. Die Experten erläutern: „5G bietet uns vor allem die Möglichkeit, innerhalb eines lokalen Funknetzwerks die Latenzzeiten zwischen Server und Client unter zehn Millisekunden zu drücken.“ Darüber hinaus müssen in der Werkstatt keine LAN-Kabel mehr verlegt werden, und die Maschinen dort können sehr flexibel aufgestellt werden.
Fabriken datensouverän digitalisieren
Von der Theorie zur Praxis ist es oftmals ein weiter Weg. Nicht so im hessischen Rittal-Werk in Haiger. Beta-Tester, produktive Anwender, Anbieter einer innovativen Edge-Cloud-Lösung und seit neuestem auch Partner im IBM-Partnerökosystem sind die Unternehmen in der Friedhelm Loh-Gruppe Rittal und German Edge Cloud (GEC).
„Im hessischen Haiger haben wir unter realen Produktionsbedingungen bei Rittal ein Testlabor für die Evaluierung und Entwicklung einer flexiblen industriellen Edge-Cloud-Umgebung aufgebaut“, berichtet Dieter Meuser, zusammen mit Dr. Sebastian Ritz CEO beim Edge-Pionier German Edge Cloud nicht ohneStolz anläslichder digitalen Hannover Messe Vorschau. Das seit 2019 auf dem Markt verfügbare innovative Edge-Cloud-Derivat Oncite von GEC wurde mit zusätzlicher kommerzieller IBM-Software bestückt und zu dem neuen Produkt „Oncite powered by IBM“ weiterentwickelt. In der High-Volume-Just-in-Sequence-Fabrik in Haiger wird es ausgiebig auf Herz und Nieren geprüft, Interessenten vorgeführt und weiterentwickelt. Meuser: „Damit verfügen wir über ein industrielles Referenzprojekt in einer realen Fabrik mit einer Vorproduktion, Lackierstraße und Endmontage, wie man sie bei jedem Automotive-OEM vorfindet.“
Beim Rittal-Werk in Haiger handelt es sich um eine typische High-Volume-Just-in-Sequence-Produktion mit 250 vernetzten Maschinen und Anlagen. Auf der PLP-Ebene (Produktionslenkungsplan als Teil der Qualitätssicherung) liegen 200 000 Datenpunkte, die rund 18 Terabyte Daten pro Tag generieren. „Im besten Fall kann Oncite per Streaming-Analyse Daten bis hin in den Petabyte-Bereich aufnehmen und ist damit allumfänglich befähigt, eine Automatisierungsplattform auch für solche High-Volume-Fabriken abzubilden“, erläutert der CEO.
Darüber hinaus verfügt das Werk Haiger auch über eine Private-Cloud-Lizenz. Das ist wichtig, nicht zuletzt für weitere Entwicklungen und Evaluierungen im Zuge der 5G-Technologie in Richtung Echtzeitfähigkeit. Meuser: „Unsere mittel- und langfristige Zielsetzung ist es, ein cyberphysikalisches System zukünftig vollständig abbilden zu können.“
Lesen Sie mehr...
Interview mit Alexander Körner (IBM-Cloud-Engagement-Hub) (PDF-Download)
Veröffentlicht in: „Produktion“
© Harald Lutz 2021
|